The first “modern” rubber gloves appeared in the late 1800s when the chief of surgery at Johns Hopkins Hospital noticed how his nurse and future wife’s hands were affected by daily contact with surgical chemicals. He commissioned a local rubber company to make a pair of reusable gloves from plaster casts of her hands.
Fast forward a few centuries, and the use of thin, disposable rubber gloves had evolved for use in a variety of industries and applications. It wasn’t until 1965 that disposable latex rubber gloves were introduced and adopted for use in the first cleanroom environments.
Finally, a century after a surgeon’s affection for his bride-to-be was the catalyst for the first rubber gloves, synthetic nitrile gloves hit the market.
Since their introduction in the 1990s, nitrile gloves have become a clean and reliable choice for cleanroom operators. Even so, latex rubber remains a popular material.
With today’s rigorous compliance and cleanliness standards for critical environments, every detail must be thoughtfully considered – down to what a cleanroom glove is made from.
Table of Content:
Why are These Factors Important?
Nitrile vs. Latex Gloves: Key Differences
Are Latex Gloves Ever Appropriate?
What is Latex Anyway?
Latex comes from the sap of rubber trees, which thrive in hot, damp regions near the equator. About 90% of global rubber production occurs in Malaysia, Thailand, Vietnam and Indonesia.
Each rubber tree is scored and tapped, releasing sap into collection containers. Collection containers are emptied into tanks and transported to a facility where the sap is blended together and put into a centrifuge to separate any proteins and potential contaminants.
It takes approximately 7 years for a rubber tree to mature enough to produce sap. Each year, the U.S. imports billions of pounds of rubber for use in tires, shoes, conveyor belts, and even gloves.
Variability in Latex
One potential problem with using latex as a glove material for use in critical environments is the variability of organic materials.
Here are a few things that impact the consistency and cleanliness of latex:
-
Age of the tree
-
Types of fertilizers and soil
-
Frequency of scoring and tapping
-
Rainfall, humidity and temperature
-
Time sap spends in the centrifuge
Each tree is different. You may be purchasing the same part number, dipped in the same facility, by the same manufacturer, but one truckload of natural latex rubber could be significantly different from the next.
Latex gloves go through on-line and off-line chlorination, however, getting an organic material to critical cleanroom standards is difficult. The cleanliness of a latex glove is heavily dependent on how well the proteins and contaminants are separated in the centrifuge. Starting with a material that’s inherently dirty means more time is spent washing and processing the gloves. That’s why “clean” latex gloves have a higher cost than any nitrile product.
Why are These Factors Important?
In addition to the risk of lot-to-lot inconsistency, latex is also an FDA-recognized allergen. Contact dermatitis is the single biggest problem with latex gloves. Statistics vary from 1% to 5% of the population has a sensitivity to either latex rubber or the proteins and potential contaminants in the organic material.
Levels of irritation vary by person. Some of the most extreme cases lead to hives, rashes, open wounds, difficulty breathing, and anaphylaxis. Other cases present as mild irritation, itchy skin, redness, and a runny nose. These reactions aren’t ideal in a critical environment where particles and contaminants must be controlled.
Today, many leading manufacturers do not let latex rubber in their facilities under any circumstance. A single operator having a serious allergic reaction is a risk. In addition to this, when facilities manufacture products that will come into contact with patients (i.e. medical devices, pharmaceutical drugs, etc.), these organizations require certification that all products used in the cleanroom environment are latex-free to avoid any downstream patient issues.
Nitrile vs. Latex Gloves: Key Differences
Nitrile, also known as synthetic latex or nitrile butadiene rubber (NBR), is an allergen-free inorganic synthetic material with many of the same desirable characteristics of latex – just without the risk of allergens. Gloves made from nitrile are comfortable, acids and solvents resistance, low in particle count, and static-dissipative.
In critical environments where tactile feedback is important, nitrile is the glove substrate of choice. Nitrile gloves have “memory technology” that allows them to conform to the human hand. Because the nitrile glove is softer, thinner, and more nimble, operators find it more comfortable and easier to use. The memory-membrane of the nitrile glove minimizes operator hand fatigue and leads to better outcomes.
Nitrile gloves also have a longer shelf-life compared to their latex counterpart. A case of nitrile gloves can last up to 5 years at minimum when stored correctly. Latex, on the other hand, ages poorly. Like an old rubber band, latex gloves will begin to brown and lose elasticity over time. Organic latex material is prone to breaking down, outgassing, and releasing contamination whereas nitrile is a more stable substrate.
Are Latex Gloves Ever Appropriate?
Let’s look at a few applications where latex is appropriate:
-
Maintenance operations: When working in an area below the cleanroom, where mechanical and electrical systems are located, it’s often preferable to use latex. This area may have vacuum pumps and tasks that require the use of sharp tools where the durability and stretchability of latex is preferred.
-
Special chemical handling: In applications where isopropyl alcohol, acetone, acids and ketones are used, latex is popular because it performs very well with solvents.
-
High voltage situations: While thin-wall gloves are not designed to be used for dealing with live transmissions, thicker latex gloves are used for electrical engineering and power distribution because latex is an insulator.
Which Glove is the Best Fit?
In Valutek’s observations, over 90% of organizations operating cleanrooms have transitioned to nitrile gloves in place of latex. However, there are certain specialty applications where latex gloves are still used.
When nitrile was first introduced in the glove market, the strength and durability factors were poor. The first 100% nitrile disposable gloves weren’t very elastic and failed certain strength and durability tests. Many organizations that haven’t recently reevaluated glove substrates are still using latex gloves that were specified decades ago.
In the last 10 years, nitrile glove formulations have improved, making them the best choice for a wide range of controlled environment applications. Nitrile offers superior performance across the three key factors of comfort, cleanliness, and cost.
When was the last time your facility qualified or requalified your glove material? Cleanroom gloves, while a seemingly minor part of any cleanroom operation’s budget, can have a disproportionate impact on yield, compliance, and outcomes.
Not sure which glove is right for you? Let Valutek make the appropriate glove recommendation based on the needs of your specific application.
EXPLORE MORE RESOURCES:
Cleanroom Glove Selection Fundamental Series | 3 Part Blog Series
From Matched Sets to Maximum Cleanliness: Gloves and Wipers in Focus | Blog
Cleanroom Catastrophes: Common Mistakes Leading to BIG Problems | Case Study
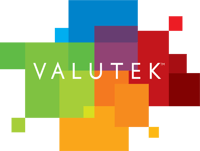
Valutek
Valutek is one of the first and few manufacturers to offer a full product portfolio of best-in-class cleanroom products. Since 1988, our controlled environment consumables are helping leading organizations operate their cleanrooms in a consistently stable state.
Related Articles
- Valutek
- 6 December 2023
From Matched Sets to Maximum Cleanliness: Gloves and Wipers in Focus
When it comes to matched sets of cleanroom products, gloves and wipers that are compatible with ...
- Valutek
- 2 November 2022
Standard Operating Procedure (SOP) Compliance Is At Risk!
Cleanroom Glove Covid-Impact White Paper And Survey Reveal Alarming Results, Offer Solutions.
There...
- Valutek
- 27 March 2023
What Hidden Contaminants in Cleanroom Gloves Put Yields at Risk?
Your cleanroom gloves help to keep your controlled environment free of contaminants. Right?
How do...